
Cement flower pot are more than just decorative containers — they represent durability, style, and sustainability. As gardening and landscaping trends continue to grow globally, the demand for high-quality cement flower pots, especially outdoor cement flower pots and large cement flower pots, is on the rise.
In this article, we’ll guide you through the manufacturing process with expert tips, share additive recommendations, and help you create better, stronger, and more appealing cement flower pots.
I.Cement Flower Pots Market Trends
Urban gardening boom: more and more people like to create balcony gardens and indoor plant collections, DIY cement planters and customized planters are becoming more and more popular.
Landscaping projects: Municipal and commercial projects use large cement planters in streetscapes, parks and public places.
Outdoor Claims: Customers need outdoor cement planters that are weather-resistant and resistant to cracking and fading.
Sustainable Appeal: Cement is a durable and environmentally friendly material that meets consumer demand for sustainable living.
For manufacturers, understanding these trends can help identify opportunities for product innovation, such as automatic watering features, custom textures and personalized mold designs.
II.Core Raw Materials and Functional Additives
1.Basic Materials
To produce high-quality cement flower pots, the core materials typically include:
Cimento Portland comum
Fine Sand (washed, sieved)
Clean Water
Optional: Lightweight aggregates (pumice, perlite) to reduce pot weight.
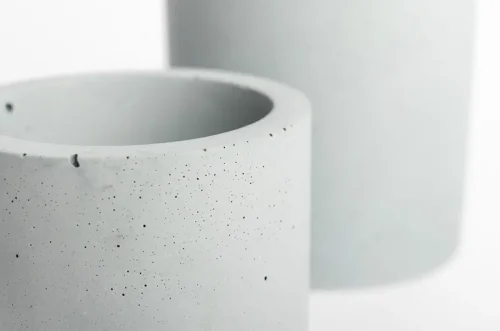
2.Recommended Additives
Pó de polímero redispersível (RDP)
Purpose: RDP improves the flexibility and adhesion of the cement mix.
Benefits:
Reduces surface cracking
Enhances weather resistance (crucial for outdoor cement flower pots)
Improves bonding with coatings or paints
Adds strength and elasticity
Cellulose Ether (HPMC/HEMC)
Purpose: Acts as a water-retaining agent and thickener
Benefits:
Improves workability and uniformity
Enhances mold release by increasing the mix’s cohesion
Reduces sagging and segregation
Helps retain moisture for proper curing, even in thin-walled cement flower pots
Additive tip: Use 1–5% RDP and 0.1–0.3% cellulose ether by dry mix weight for optimal performance.
III.Manufacturing Process of Cement Flower Pots
1.Step 1 – Precise Mix Design
A well-balanced mix is the foundation of every successful cement pot.
Here’s a professional recommendation:
Water-cement ratio = 0.4 to 0.5
RDP: 1–5% of total dry weight
HPMC: 0.1–0.3%
The right mix ensures:
Smooth flow into molds
Reduced air bubbles
Stronger final product with fewer cracks
2.Step 2 – Mold Selection and Preparation
Choosing the correct cement flower pot molds affects the design, surface finish, and ease of demolding.
Types of molds:
Plastic molds – cost-effective, good for volume production
Silicone molds – flexible and detailed, great for custom shapes
Steel molds – durable, ideal for large cement flower pots
Preparation tips:
Clean and dry molds before each use
Apply a thin layer of mold release agent
Ensure all molds are level and leak-free

3.Step 3 – Casting and Curing
Once your mix is ready:
Pour slowly into the mold to avoid trapped air
Use a vibrating table to remove bubbles and settle the mix
Smooth the top surface and tap sides to eliminate air pockets
Curing process:
Cover with plastic or damp cloth
Keep moist and shaded for 48–72 hours
Proper curing ensures strength and reduces shrinkage cracks
RDP and HPMC additives help retain internal moisture and prevent early cracking during this crucial phase.
4.Step 4 – Demolding and Surface Finishing
Once cured:
Carefully remove the mold, starting from the edges
HPMC improves demolding smoothness and reduces sticking
Let the pot dry fully before any surface treatment
Finishing options:
Sanding for a matte or smooth finish
Painting or staining with water-based colors
Applying sealers for waterproofing and long-lasting color
Additives like RDP also improve the adhesion of coatings, enhancing durability and aesthetics.
IV.Performance Enhancement Through Additives
1.Why RDP matters:
Reduces water absorption and cracking
Improves flexibility and weather resistance
Increases product lifespan for outdoor cement flower pots
2.Why Cellulose Ether (HPMC/HEMC) matters:
Stabilizes the mix and prevents segregation
Improves consistency during casting
Aids in controlled curing and hydration
Enhances demolding and surface texture
In short: If you want a high-end, crack-free, professional cement flower pot, additives are essential.

V.Common Problems and Solutions
Problema | Likely Cause | Solução |
Cracks in the pot | Shrinkage or poor curing | Add RDP and improve curing conditions |
Air bubbles on surface | Poor mix or insufficient vibration | Use vibrating table and ensure proper fluidity with HPMC |
Mold sticking | No mold release or low-quality mix | Use mold release and cellulose ether for better cohesion |
Weak structure | Incorrect mix or poor hydration | Adjust water ratio, add RDP, extend curing time |
VI. Conclusão
Making high-quality cement flower pots involves more than just mixing cement and pouring it into a mold. To stand out in today’s market, manufacturers must use the right materials, adopt smart production methods, and include performance-enhancing additives like RDP and HPMC.
By upgrading your formulas and optimizing your process, you can produce DIY cement flower pots, outdoor cement flower pots, and large cement flower pots that delight customers and last for years.