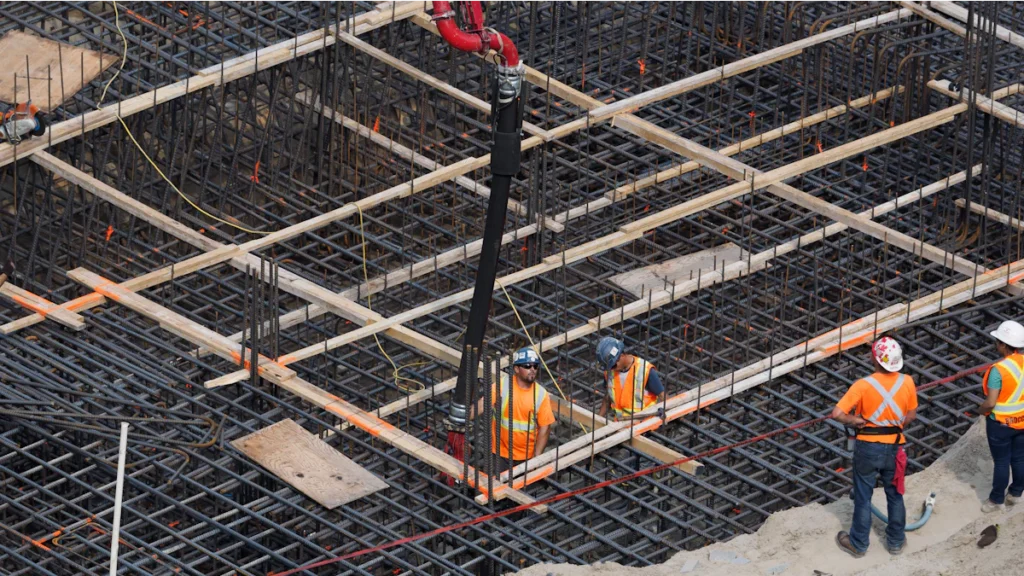
Choosing between HPMC vs HEMC depends on the specific requirements of the project. Both cellulose ethers have unique properties that lend themselves to a variety of applications. HPMC is known for its excellent water retention and processability and is widely used in the construction and pharmaceutical sectors. HEMC, on the other hand, has excellent water retention and a smoother consistency, making it ideal for high-temperature environments. The choice ultimately depends on the desired outcome and project needs. Understanding these differences can help select the right material for optimal performance.
I. Understanding HPMC vs HEMC
Both HPMC and HEMC are cellulose ethers with excellent water retention, thickening and bonding properties, but their chemical composition and applications are different.
1. Chemical Composition
2. Key Properties
Solubility
Both HPMC and HEMC are water soluble, but they differ in their dispersibility. HEMC is more water soluble than HPMC and disperses better in water. This property makes HEMC particularly suitable for applications that require fast and efficient mixing. In contrast, HPMC’s solubility supports its role as a stabilizer and emulsifier, especially in formulations where controlled release and consistency are critical.
Viscosity
Viscosity is a key factor in determining the performance of HPMC vs HEMC. HPMC has a wide range of viscosities, from 400 to 200,000 mPa.s, making it suitable for a variety of uses. Its ability to enhance viscosity and adhesion is suitable for construction applications such as tile adhesives and wall putties. HEMC has excellent thickening and bonding properties. This makes it ideal for high temperature environments and applications that require a smooth consistency. Both cellulose ethers are effective thickeners, but their specific viscosity properties may affect selection depending on project needs.
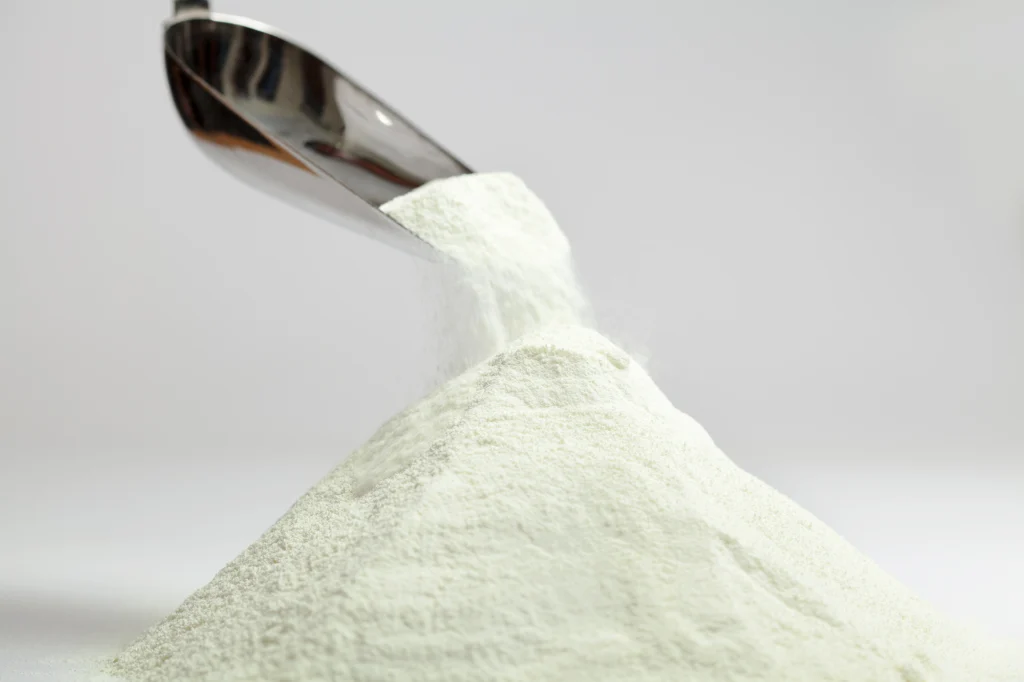
II. Functions and Applications
1. Construction Uses
Application of HPMC in Construction
Application of HEMC in Construction
Hydroxyethyl methylcellulose (HEMC) has unique advantages in construction, especially in environments that require high thermal stability. Its excellent water retention and smoother consistency make it ideal for exterior applications, such as cement tile adhesives and wall putties. HEMC contains hydroxyethyl and methyl groups, which are more advantageous in water solubility and less sensitive to salt. HEMC’s enhanced resistance to alkaline environments ensures that it performs well in mortar and cement mixes. HEMC’s higher gel temperature provides better resistance to sagging, which is essential for maintaining the integrity of vertical surfaces. These properties make HEMC a reliable choice for construction projects that require stability under harsh conditions.
2. Other Industry Applications
HPMC Applications
Because of its adaptability, HPMC is utilized in a variety of industries in addition to building. In the pharmaceutical sector, HPMC can be used as a binder and film former in tablet formulations, ensuring the controlled release of active ingredients. HPMC’s non-toxic nature and high gel strength make it suitable for personal care products, where it is used as a thickener and stabilizer in creams and lotions. HPMC’s ability to dissolve in cold water and form colloidal solutions also makes it valuable in the food industry, where it is used as an emulsifier and stabilizer in processed foods.
HEMC Applications
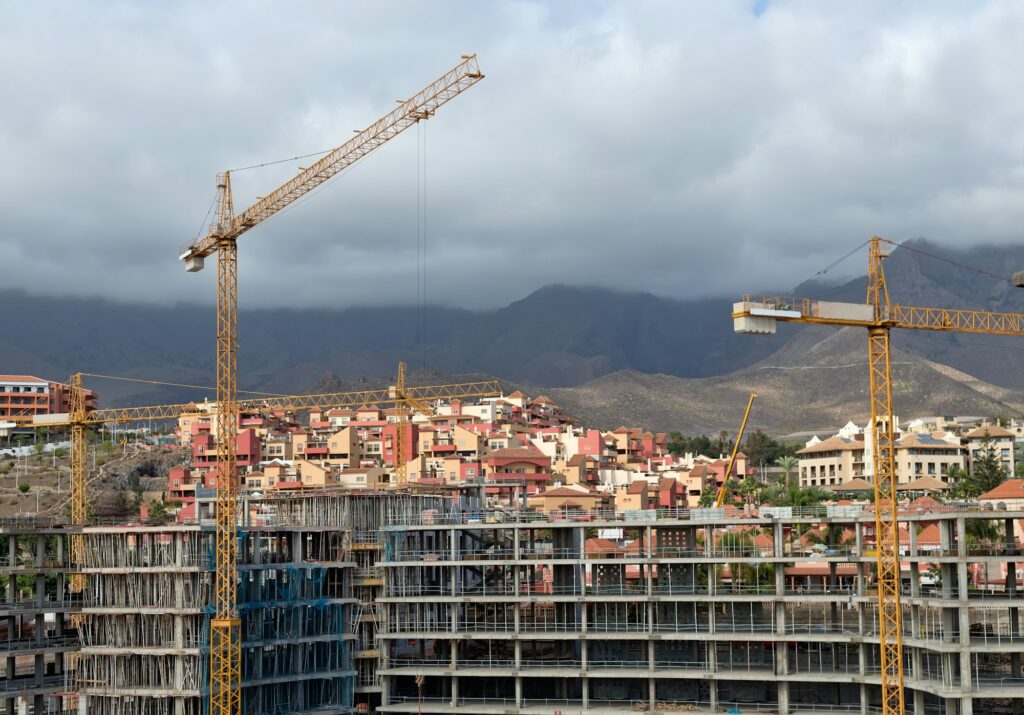
III. How to choose HPMC vs HEMC
In order to better decide the choice of HPMC or HEMC, here are some key selection methods to help you make a wise choice under different project requirements and environmental conditions:
1. Choose according to the type of substrate
- Cement-based applications (such as tile adhesives, wall putties) are more suitable for HPMC because it provides excellent water retention and fluidity, prolongs the open time, and helps the bonding effect.
- Gypsum-based products (such as gypsum mortar, gypsum-based leveling materials) are more suitable for HEMC, and its stability and salt resistance in highly alkaline environments make it perform better in such products.
2. Environmental conditions
- If the construction environment is in coastal areas or high humidity and high salt environments, it would be more appropriate to choose HEMC. HEMC has stronger salt and alkali resistance and can effectively resist the influence of the external environment.
- In conventional construction environments, HPMC’s performance is usually good enough, so it is an ideal choice at a relatively lower cost.
3. Requirements for construction performance
- If your project requires good fluidity and longer open time (such as tile adhesive or wall putty), HPMC would be a better choice. It can provide smooth workability, facilitate construction and improve efficiency.
- If the construction requires higher viscosity and shaping ability (such as gypsum-based mortar), HEMC has stronger applicability and can better support the need for vertical stability in construction.
In summary, HPMC and HEMC each have unique advantages to meet the needs of specific projects. HPMC excels in water retention and processability, making it an ideal choice for construction and pharmaceutical applications. HEMC has excellent thermal stability and a smoother consistency, suitable for high temperature environments and harsh construction conditions. The choice between these cellulose ethers depends on the specific requirements of the project. By understanding these differences, you can ensure the best performance and durability of their applications.