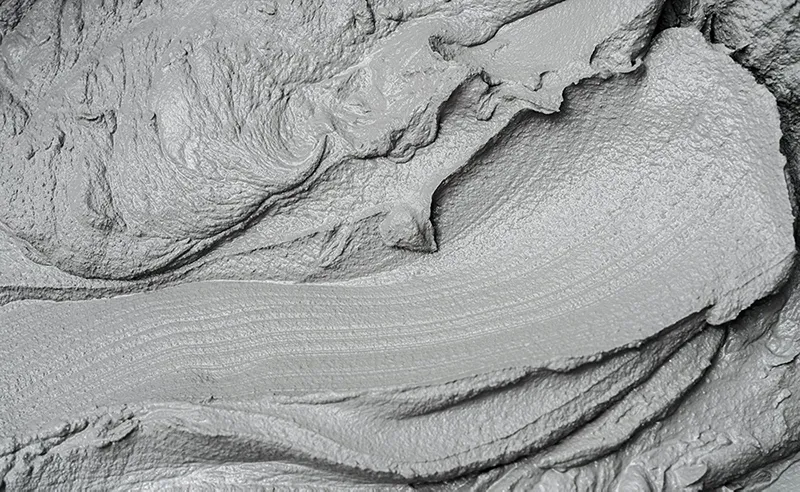
Dry mix mortar formulations can provide pre-mixed solutions with high efficiency, consistency and high performance. Unlike traditional field-mixed mortars, dry mix mortars are carefully formulated to meet specific application needs, ensuring optimal workability, durability and adhesion strength.
In this article, we will explore the key considerations in dry-mix mortar formulations and focus on two basic types: waterproof mortars and insulation mortars.
I.Understand the dry mix mortar formula
Dry-mix mortar formulations consist of adhesion,aggregates and functional additives. The right combination of these ingredients determines the strength, flexibility, adhesion, water resistance, and thermal properties of the final product.
Adhesion: The most common adhesion are cement, lime, and gypsum, which provide strength and adhesive force
Aggregates: Sand, lightweight fillers, or expansive materials help increase density and workability.
Additives: Cellulose ethers, redispersible ploymer powders, high-efficiency water reducers, and retarders enhance water retention, adhesion, and setting time, among other things.
By adjusting these ingredients, manufacturers can fine-tune mortar formulations to meet different environmental conditions and application needs.
II.Waterproof mortar formula
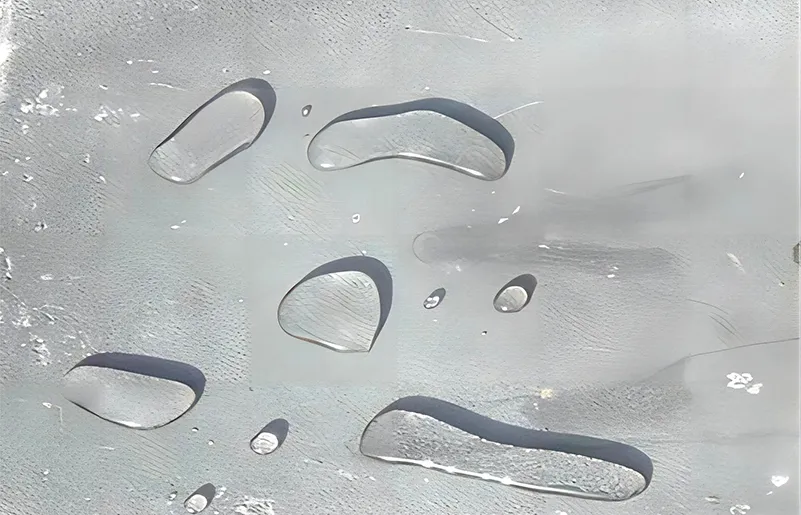
1.Key requirements for waterproofing mortar
Waterproofing mortar is used in areas exposed to moisture such as bathrooms, basements, swimming pools and exterior walls. The main objectives of waterproofing mortar are:
Low water absorption to prevent moisture penetration.
High durability to withstand harsh environmental conditions.
Excellent adhesion to various substrates to prevent delamination.
2.Basic ingredients and formula in waterproof mortar
Adhesion: A combination of cement and supplementary cementitious materials (SCM) such as fly ash or silica fume increases density and reduces permeability.
Hydrophobes: Silicone additives, water-repellent polymers or crystalline admixtures help prevent water absorption and improve long-term durability.
Cellulose ethers (HPMC/HEMC): These additives improve water retention, workability and crack resistance, ensuring smooth and stable construction.
Right amount of sand: The right amount of sand reduces voids and increases the density of the mortar, thereby reducing water infiltration.
Suroviny | Hmotnost/kg |
Ordinary Portland Cement(PO 42.5) | 450 |
Sand(0.1-0.8mm) | 520 |
Hydroxypropyl Methyl Cellulose | 1.5-2 |
Silikonový hydrofobní prášek (SHP) | 2 |
Redispergovatelný polymerní prášek (RDP) | 20-25kg or more |
Polykarboxylátový superplastifikátor (PCE) | 1-2 |
Odpěňovač prášku | 1-2 |
1000 |
3.Optimization Strategies
To improve the performance of waterproofing mortars, manufacturers should:
Adjust the adhesion-to-aggregate ratio to balance strength and permeability.
Use polymer modification systems to enhance flexibility and adhesion.
Test water absorption and resistance to penetration to ensure long-term waterproofing performance.
Waterproofing mortars are especially important for projects that require prolonged exposure to moisture. A well-formulated mix can prevent water-related damage, significantly extending the life of buildings and infrastructure.
III. Thermal insulation mortar formula
1. Insulation mortar

Insulation mortar is designed to reduce heat transfer, making it an ideal choice for exterior insulation finish systems (EIFS), interior wall coatings, and energy-efficient building envelopes. The following are the basic properties of insulation mortar:
Low thermal conductivity to minimize heat loss.
Lightweight composition to reduce structural loads.
Strong adhesion to ensure durability and prevent cracking.
2.Basic ingredients and formula of thermal insulation mortar
Lightweight Aggregates: Expanded perlite, EPS (expanded polystyrene) particles and vitrified microspheres help achieve low-density mortars with high thermal insulation performance.
Adhesion: Use cement, fly ash or gypsum-based adhesive to provide structural integrity while maintaining low thermal conductivity.
Cellulose ethers: Improve workability, prevent segregation, and enhance the adhesion of lightweight fillers.
Redispersible polymer powders: Improve adhesion to insulation boards and masonry surfaces, preventing cracking or flaking.
Polypropylene fibers: Enhance the crack resistance of mortars.
3.Optimization Strategies
Suroviny | Hmotnost/kg |
Ordinary Portland Cement(PO 42.5) | 500 |
Fly Ash(second level) | 300 |
Fine Sand | 200 |
Redispergovatelný polymerní prášek | 8-15 |
Hydroxypropylmethylcelulóza | 3-4 |
Polypropylene Fiber (6mm) | 1 |
Slurry | Polystyrene granules (25kg powder per bag, 0.1-0.15m3) |
Vitrified microspheres (25 kg powder per bag,10-13 kg ) | |
Perlite (25 kg powder per bag, about 5-6 kg per bag) |
To improve the performance of thermal insulation mortar:
Fine-tune density to balance insulation and mechanical strength.
Use fiber reinforcement to prevent shrinkage cracks.
Ensure compatibility with exterior wall systems (EIFS) for long-term stability.
Insulation mortar is widely used in green building projects and energy-efficient construction. Customized formulations enable optimal performance in different climates and structural conditions.
IV.Adjust the formulation to the application needs
Dry-mix mortars must be adjusted to the specific project requirements, environmental factors and application techniques. Considerations include:
Climate adaptation:
In hot climates, retarders are added to prevent premature setting.
In cold regions, accelerators help maintain the speed of cure.
Substrate compatibility:
For smooth surfaces such as glass or metal, special adhesion promoters may be required.
For porous materials, primers can improve adhesion strength.
V.Testing and quality control of dry-mix mortars
To ensure a high-quality formulation, laboratory and field testing is essential.
Key tests for performance verification:
Compressive strength test – ensures that the mortar can withstand structural loads.
Adhesion strength test – measures the bond between the mortar and the substrate.
Water absorption test – determines the moisture resistance of the mortar.
Thermal conductivity test – evaluates the insulation efficiency.
Regular quality control prevents inconsistencies and ensures that the mortar performs as expected in the actual application.
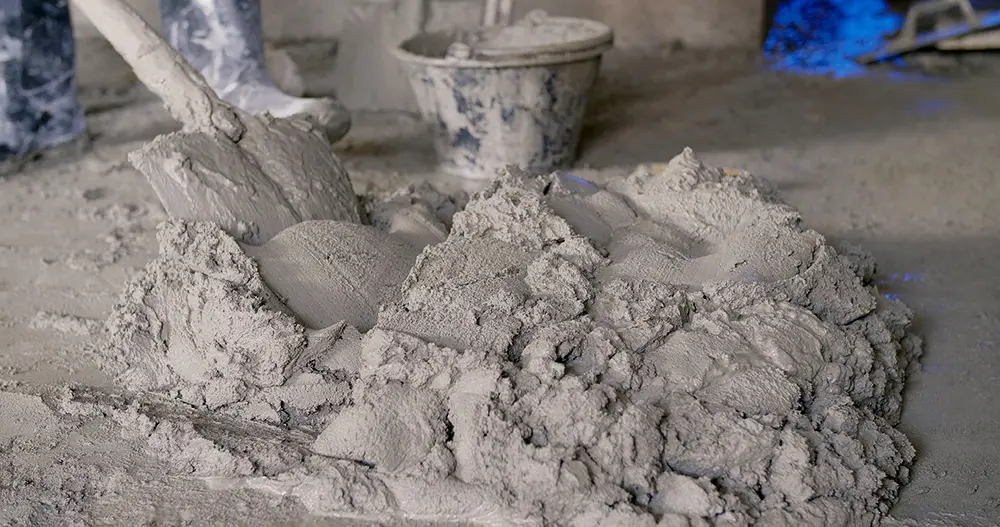